Contributed by Carol Hunt, International Parts Sales Rep
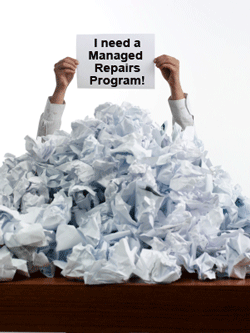
Managed Repairs Programs manage all aspects of aircraft parts repairs so you can focus on other important things.
An Aircraft Parts Managed Repairs Program helps operators to better manage their aircraft parts repair maintenance projects by streamlining the quote process, cutting through red tape and consolidating unit shipping. The program manages all aspects of aircraft parts repairs from quote to delivery, giving operators the freedom to focus on other important aspects of operating their aircraft.
Before you continue to ship multiple aircraft units to different locations, explore the advantages of an Aircraft Parts Managed Repairs Program.
One Point of Contact
A Managed Repairs Program contacts all vendors and consolidates quotes into one proposal. No matter how many units you ship for repair, you only review and approve one contract. The program will manage all vendor warranties for each unit.
Advanced Customs Clearance
Providing part and serial numbers to program administrators in advance of shipping the units can save you as much as two weeks shipping time and high import fees. A Managed Repairs Program can assist with pre-clearance through U.S. Customs for all units sent into the U.S.for maintenance.
Consolidated Freight Charges
Operators utilizing an Aircraft Parts Managed Repairs program may ship all units scheduled for repair to one location, eliminating the hassle of managing multiple addresses and contacts. After overhaul or repair, all units are returned in one shipment or according to operator’s requirements.
Advanced Shipping Notice & Control
As an operator, you are free to determine how and when your units are returned.
No Hidden Terms
With a Managed Repairs Program there are no hidden terms or fees. All payment terms are determined up front, prior to return shipment.
Duncan Aviation offers an Aircraft Parts Managed Repairs program, free to all operators who want to reduce paperwork, minimize freight costs and get faster results. They provided extensive repair and overhaul services—including exchanges—for business aircraft parts, avionics, instruments, accessories and propellers. We maintain a large inventory of business aircraft parts for sale. We also hold more than 70 manufacturer authorizations for avionics, instruments, accessories and propeller units.
Carol Hunt, International Parts Sales Repspecializes in locating aircraft parts in the international market and assisting operators in all countries through the maze of aircraft parts maintenance. Her aviation career began in 1979.