 |
501-1228-04: Lead Acid Emergency Power Supply |
If you are waiting more than two weeks for an offer on your available aircraft avionics inventory, you are waiting too long.
The business aviation industry is growing rapidly and the demand for good, serviceable avionics parts to support customers’ current and future needs is strong. So Duncan Aviation’s Parts & Rotables Sales has stepped up efforts and increased on-hand inventory of avionics parts for all makes of business aircraft, including modifications packages removed for avionics upgrades.
Every day, customers reach out to Avionics Acquisitions Manager, Jamie Blackman, and her team offering a list of inventory to purchase. Most lists average 20-50 part numbers, but can be as high as 5,000.
- Aircraft inventory companies that purchase aircraft to part-out offer us avionics units, knowing our customer base will likely be able to use the inventory.
- DOMs will sell their rotable pools if their aircraft is traded in for a larger or newer aircraft. These pools consist of good, serviceable units they no longer need. So they sell the units and then turn around and buy inventory for their new rotable needs.
“We have no limits on how large or small of a list we’ll buy,” says Jamie. “If a customer presents us with a list, we’ll take it all whether we have repair capabilities or not.” This makes it easier for the customer, she says, saving them the time it takes to go to multiple outlets to sell their inventory.
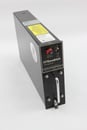 |
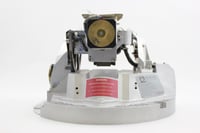 |
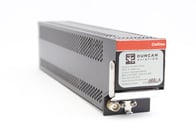 |
501-1712-02: Emergency Power Supply |
071-01519-0101: King Ant/RCVR/XMTR |
622-1270-001: Collins Transponder |

Best Price First
But they won’t haggle on price and Jamie explains why, “We always offer our best price out of the gate, never low-balling or engaging in time-consuming negotiations. We won’t waste your valuable time exchanging emails or phone calls to come to pricing terms. By offering your the fairest price upfront, we save ourselves time and make you money.”
William Calgagni of the Calin Corporation explains why he selected Duncan Aviation to sell his avionics parts. “Out of the three companies I contacted, Duncan Aviation was the easiest to work with and the best fit for my needs, offering a competitive price.”
Jamie knows by offering the fairest price upfront the seller is more likely to come back again the next time they have additional units for sale. William agrees, “The next time I have any avionics units to sell, Duncan Aviation will be on the short list again.”
“We are more than happy to explain how we arrived at our offer,” explains Jamie. When a list is received, it is examined and compared to all of the historical data that has been collected by Duncan Aviation. Each Individual part number is researched to find sales history as well as repair capabilities and average repair costs. Even our own stock quantities are examined to determine the current number of units on hand. All of this information together provides the most accurate fair market value and is used to formulate the purchase offer extended to the customer.
Our offers are competitive and, in most cases, higher than others because we have more than 45,000 different repair manuals and a large team of avionics repair professionals. These in-house repair capabilities keep costs under control, allowing us to offer more money for the units. And our wide and active customer base ensures that we are able to maintain multiple units in our inventory.
Best Price Fast
 |
071-01550-0101: King Radar Antenna |
Not only will you get our best offer out of the gate, you’ll have that offer within one to two business days of receiving the list. There is no waiting up to two weeks to hear back about an offer or to find out that most of the list is rejected. We have a proprietary computer program that compares individual part numbers to Duncan Aviation’s entire historical experience with each unit. With a click of a button, we are able to replicate the thoroughness of manual line-by-line research, but have results within a matter of a few hours.
Over the past three years, the Duncan Aviation Parts & Rotable Sales has added over $2.5 million in avionics inventory. And recently started an Avionics Purchasing Program to build an inventory of avionics units for which we don’t have repair capabilities. “The market demand for these newer systems is beginning to grow,” says Jamie. “Our customers need these units and we want to be able meet those needs by being their best source.”
WeBuyAvionics@DuncanAviation.com
If you have avionics inventory, whether it is one unit or thousands of piece parts, we will be the first to respond and with the best offer. When receiving your payment you have the option of cash, trade or putting credit on your account for future Duncan Aviation work, anywhere in the company.
Contact Duncan Aviation to sell your excess avionics inventory by emailing an Excel spreadsheet of your parts list, including part numbers to WeBuyAvionics@DuncanAviation.com. We are also interested in purchasing surplus inventories of airframe and engine accessory components.